What is Porosity in Welding: Important Tips for Achieving Flawless Welds
The Scientific Research Behind Porosity: A Comprehensive Overview for Welders and Fabricators
Understanding the detailed systems behind porosity in welding is essential for welders and makers pursuing impressive craftsmanship. As metalworkers dive into the depths of this sensation, they reveal a world governed by different variables that affect the development of these tiny spaces within welds. From the structure of the base products to the complexities of the welding process itself, a multitude of variables conspire to either exacerbate or ease the presence of porosity. In this extensive guide, we will unravel the science behind porosity, discovering its results on weld top quality and unveiling advanced techniques for its control. Join us on this trip with the microcosm of welding flaws, where accuracy meets understanding in the quest of flawless welds.
Comprehending Porosity in Welding
FIRST SENTENCE:
Evaluation of porosity in welding reveals important insights into the honesty and top quality of the weld joint. Porosity, defined by the presence of tooth cavities or gaps within the weld steel, is an usual concern in welding procedures. These voids, otherwise appropriately resolved, can compromise the structural stability and mechanical properties of the weld, resulting in possible failures in the ended up item.

To spot and quantify porosity, non-destructive screening techniques such as ultrasonic screening or X-ray inspection are often employed. These techniques enable the identification of internal flaws without endangering the honesty of the weld. By analyzing the size, shape, and circulation of porosity within a weld, welders can make educated choices to improve their welding processes and accomplish sounder weld joints.

Aspects Affecting Porosity Development
The occurrence of porosity in welding is affected by a myriad of factors, varying from gas shielding efficiency to the details of welding criterion setups. Welding specifications, including voltage, existing, take a trip rate, and electrode type, likewise influence porosity development. The welding strategy used, such as gas steel arc welding (GMAW) or protected metal arc welding (SMAW), can influence porosity formation due to variants in warm distribution and address gas insurance coverage - What is Porosity.
Impacts of Porosity on Weld High Quality
The existence of porosity likewise damages the weld's resistance to deterioration, as the entraped air or gases within the spaces can react with the surrounding atmosphere, leading to deterioration over time. Additionally, porosity can prevent the weld's capacity to endure pressure or influence, further endangering the overall quality and dependability of the welded framework. In crucial applications such as aerospace, automobile, or structural buildings, where safety and durability are extremely important, the harmful effects of porosity on weld quality can have severe consequences, highlighting the relevance of lessening porosity via proper their website welding methods and treatments.
Strategies to Minimize Porosity
In addition, utilizing the proper welding specifications, such as the right voltage, current, and take a trip speed, is important in protecting against porosity. Keeping a regular arc size and angle during welding likewise aids minimize the chance of porosity.

Using the proper welding strategy, such as back-stepping or using a weaving motion, can additionally assist disperse warmth evenly and decrease the opportunities of porosity development. By implementing these strategies, welders can efficiently minimize porosity and produce high-quality welded joints.
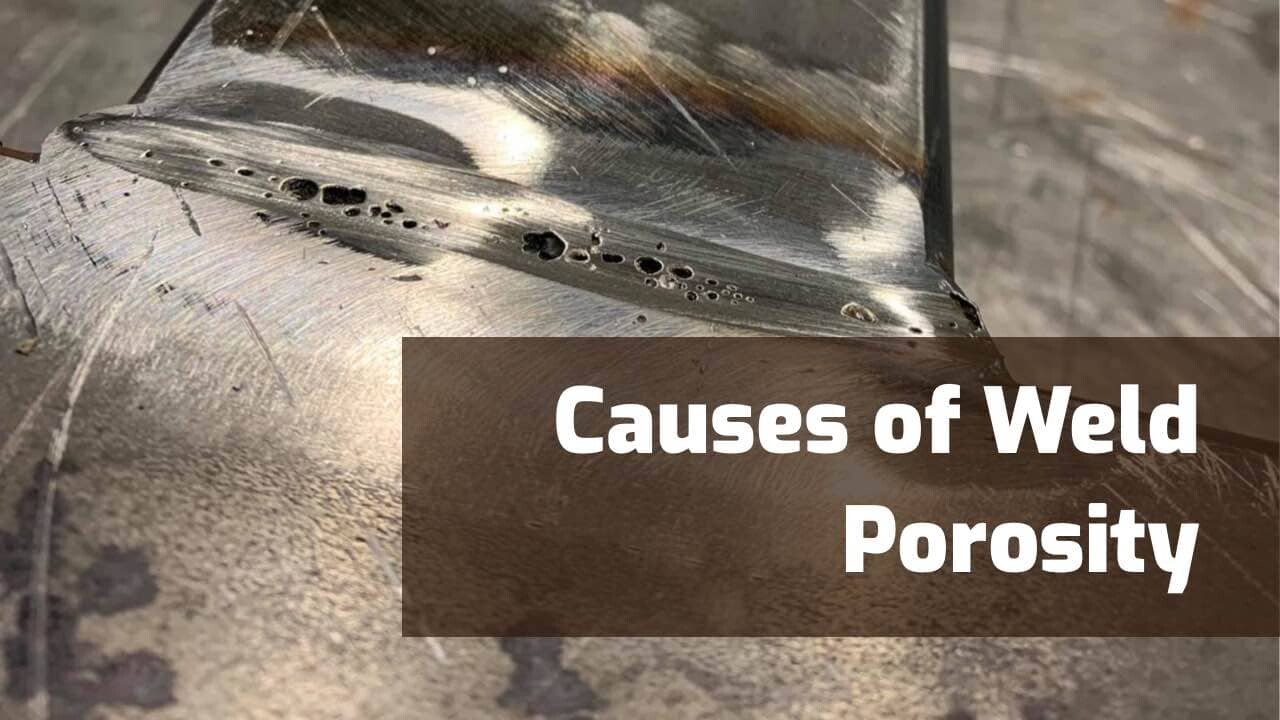
Advanced Solutions for Porosity Control
Applying cutting-edge modern technologies and innovative approaches plays an essential duty in accomplishing remarkable control over porosity in welding processes. One innovative remedy is making use of innovative gas mixes. Securing gases like helium or a mix of argon and hydrogen can help in reducing porosity by offering much better arc stability and boosted gas insurance coverage. Furthermore, using sophisticated welding techniques such as pulsed MIG welding or customized atmosphere welding can also assist minimize porosity issues.
One more advanced remedy includes using advanced welding devices. For example, making use of equipment with integrated attributes like waveform control and sophisticated source of power can improve weld top quality and lower porosity threats. Additionally, the implementation of automated welding systems with specific control over criteria can considerably lessen porosity flaws.
Moreover, integrating sophisticated monitoring and evaluation innovations such as real-time X-ray imaging or automated ultrasonic testing can assist in detecting porosity early in the welding process, permitting instant corrective actions. Generally, incorporating these read the article innovative services can substantially improve porosity control and enhance the total high quality of bonded components.
Final Thought
In verdict, understanding the science behind porosity in welding is important for welders and makers to create high-grade welds - What is Porosity. Advanced services for porosity control can even more enhance the welding procedure and ensure a strong and trusted weld.